Introduction: In today’s world, energy efficiency is a paramount concern across various industries. It not only helps reduce operational costs but also contributes to environmental sustainability. Vibratory feeder controllers play a crucial role in industries such as manufacturing, mining, and agriculture by transporting bulk materials efficiently. One key method to enhance the energy efficiency of vibratory feeder controllers is through the implementation of Frequency Modulation (FM) techniques. In this blog, we will explore the significance of FM in optimizing energy usage in vibratory feeder controllers and its potential benefits for your industry.
Understanding Vibratory Feeder Controllers
Vibratory feeders are widely used in various industrial applications to transport and convey materials like granules, powders, and parts. These feeders rely on electromechanical systems to generate vibrations, which move materials along a predefined path. The heart of the vibratory feeder system is the controller, which dictates the operation of the feeder unit. Traditional feeder controllers typically operate at a fixed frequency, which can lead to energy wastage and reduced control precision.
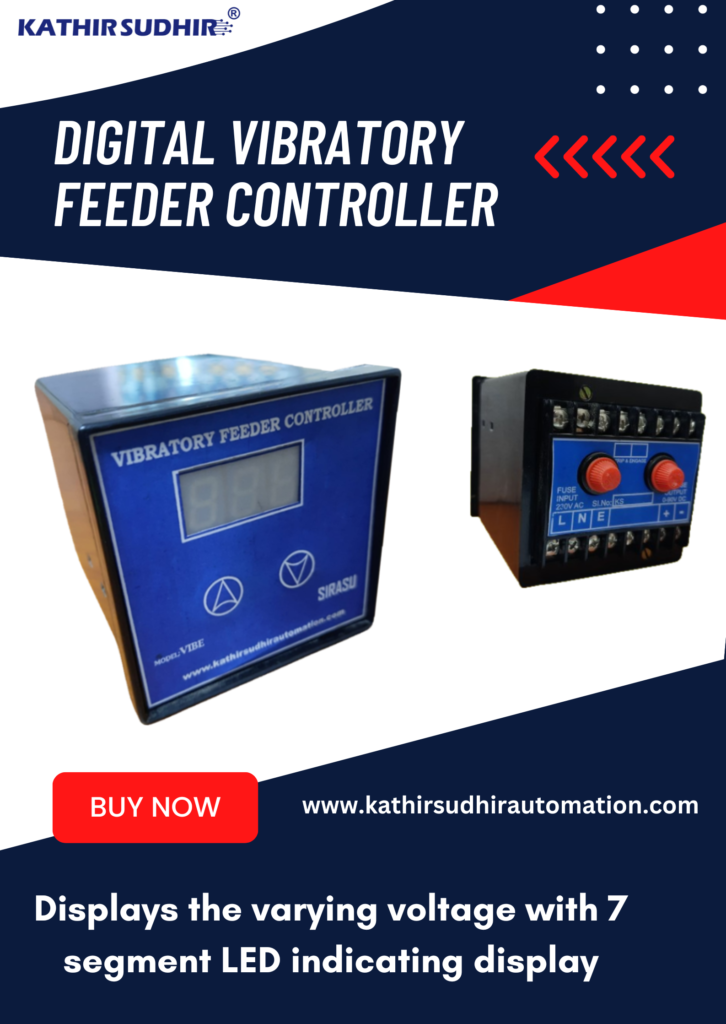
Frequency Modulation: A Game-Changer for Energy Efficiency
Frequency Modulation (FM) involves altering the operating frequency of the vibratory feeder controllers dynamically. Unlike traditional fixed-frequency controllers, FM allows for continuous adjustment of the vibration frequency. Here’s how FM can significantly enhance energy efficiency in vibratory feeders:
- Load Adaptability: FM controllers can adapt to varying load conditions. When the feeder is handling a lighter load, the controller can lower the frequency to conserve energy. Conversely, when dealing with a heavy load, it can increase the frequency for optimal material transport, reducing the risk of jams and overloads.
- Reduced Energy Peaks: Fixed-frequency controllers often experience energy spikes during startup or when handling difficult-to-convey materials. FM smoothens these peaks by adjusting the frequency as needed, preventing energy wastage.
- Precise Material Control: FM controllers enable precise control over the material flow rate. This ensures that materials are transported efficiently and evenly, reducing the likelihood of spillage, waste, and product damage.
- Extended Equipment Lifespan: By reducing the stress and strain on the equipment, FM controllers can extend the lifespan of vibratory feeders, ultimately saving on maintenance and replacement costs.
- Lower Operational Costs: Improved energy efficiency leads to reduced energy bills, making FM controllers a cost-effective choice for businesses looking to optimize their operations.
Implementing FM in Vibratory Feeder Controllers
To implement Frequency Modulation in your vibratory feeder controllers, consider the following steps:
- Controller Upgrade: Replace or retrofit your existing fixed-frequency controllers with FM-enabled ones. This may involve installing new hardware and updating control software.
- Parameter Tuning: Fine-tune the FM controller parameters to match the specific requirements of your application. Factors like material type, load, and conveyor length will influence these settings.
- Monitoring and Maintenance: Regularly monitor the performance of your FM controllers and conduct preventive maintenance to ensure optimal operation and longevity.
Conclusion
Frequency Modulation offers a promising solution for enhancing energy efficiency in vibratory feeder controllers across various industries. By optimizing material handling processes, reducing energy wastage, and improving control precision, FM controllers not only save costs but also contribute to sustainable industrial practices. As businesses continue to prioritize energy efficiency, the adoption of FM technology in vibratory feeder controllers is a logical step forward for a greener, more cost-effective future.